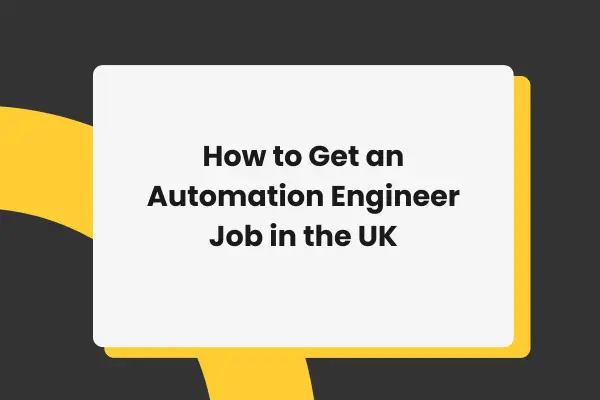
Overcoming Steel Tariffs: How OEMs Are Adapting in the Process & Packaging Industry
Original Equipment Manufacturers (OEMs) in the process and packaging sector are facing mounting pressure due to the latest US tariffs on imported steel.
As steel remains a core material in machinery production, these new trade regulations have the potential to significantly impact cost structures, lead times, and supplier relationships. However, OEMs are not standing still. Instead, they are responding with a multi-pronged approach that balances operational efficiency, product innovation, and strategic planning.
One of the most immediate responses from OEMs has been the diversification of their steel sourcing strategies. Many have turned to domestic suppliers to bypass the tariffs entirely, strengthening local partnerships and investing in regional supply networks. Where domestic options fall short, OEMs are exploring countries with favourable trade agreements or those exempt from the tariffs. This approach reduces exposure to elevated costs and increases flexibility in procurement.
To complement their sourcing strategies, OEMs are optimising their supply chains. This includes reshoring certain production activities closer to key markets, which helps reduce transportation costs and tariff-related expenses. Manufacturers are also doubling down on lean practices, minimising waste, and improving workflow efficiency to balance out the financial impact of higher steel prices.
Improved inventory management has become essential, with companies adjusting stock levels to cushion against pricing volatility and potential disruptions.
Product innovation is also playing a critical role. Engineers are working to reduce steel usage in equipment designs by trimming weight and rethinking structural requirements. In some cases, alternative materials such as aluminium or composites are being introduced where suitable, which not only decreases reliance on steel but can also open the door to new design possibilities.
Modular equipment designs are gaining traction too, offering more flexibility in component sourcing and allowing OEMs to adapt to changing material availability.
On the commercial side, many OEMs are renegotiating contracts with suppliers to secure more favourable terms. Some are leveraging long-term relationships or volume commitments to offset price hikes.
In situations where cost absorption is not feasible, manufacturers may need to pass a portion of these costs to their customers, particularly when dealing with highly customised or advanced equipment. For some OEMs, seeking tariff exemptions or waivers is also a practical route, especially if the equipment or its components meet specific criteria under trade regulations.
Beyond immediate actions, OEMs are staying vigilant. Monitoring global trade developments, shifting policy trends, and engaging in scenario planning allows them to remain agile. Many are also working closely with industry associations to advocate for policy changes and share resources that help members navigate the shifting landscape.
For clients in the process and packaging industry, understanding how your OEM partners are adapting to these pressures is essential. The steps they are taking not only ensure continuity and stability but also reflect a commitment to innovation and long-term value in an increasingly complex global market.
To stay up to date on industry challenges, open roles and insight, head to our process and packaging page.